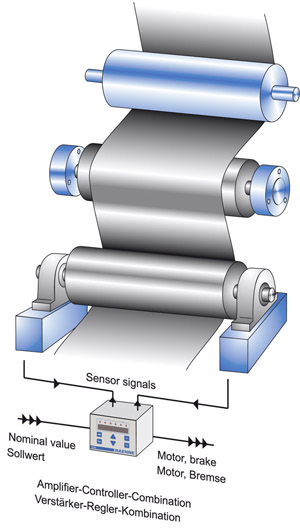
Web Tension Measurement Systems
In processes where running webs of material are continuously manufactured with increasing process speeds and higher demands on quality it is necessary to measure and control the tension forces in the material. This applies equally well to the production and converting of plastic foil, textiles, paper, and metal as well as wires and cables.
Because the forces cannot be measured directly in those in running webs it is necessary to measure the forces acting on the bearings of idler rolls. The measured values are proportional to web tension if the systems are correctly dimensioned.
Because of possible non symmetrical load distribution over the rolls it is customary to measure the forces in both bearings of the idler roll. The core of the web tension sensors are strain gauge transducers measuring the acting forces. Amplifiers, increasingly common with digital fieldbus interfaces, raise the very low sensor signals to the appropriate levels.
The „standard“ measuring system consists of two sensors and one amplifier. The second sensor is not necessary if the web runs steady in the middle of the rolls and the process does not require high precision web tension measurement. The analog output of the amplifier can be either voltage or current signals. Depending upon the sensor cable length the amplifiers are either housed in field enclosures mounted close to the sensors or alternatively DIN rail enclosures are available for mounting in electrical cabinets.
However, when using an additional fieldbus amplifier the force values of each sensor can be used to determine e. g. the differential web tension of the system. If fieldbus amplifiers are used, then the force values can be send directly onto the fieldbus.